践行精益管理3年多,一机集团正从内向外发生着精彩“蝶变”。
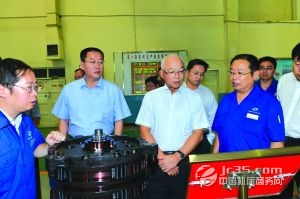
中国兵器工业集团董事长、党组书记尹家绪(左三)在一机集团听取解精益生产示范岗所取得的改善效果。
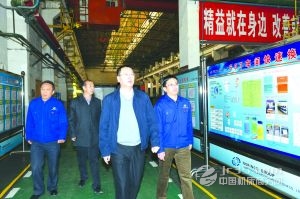
一机集团董事长、党委书记白晓光深入生产现场检查精益管理工作开展情况。
多年来,作为声名赫赫的老牌军工企业,内蒙古一机集团虽然连续保持盈利,但随着民营企业在制造领域的迅猛崛起,计划经济体制下形成的种种弊端却开始逐步显现:制造成本率高、获利能力偏低、“两金”占用高、全员劳动生产率低、价值创造能力不强、资源使用效率不高、市场竞争力下降等等问题都在倒逼企业思考:如何以前瞻的理念和最前沿的现代化管理手段跟上时代发展的步伐,消除生产和管理流程中的浪费和不增值现象,提升各环节的价值创造能力,使一机集团重新焕发生机与活力,为国家兵器工业的崛起作出更大的贡献?
国际宏观经济形势的复杂多变,国内改革的紧迫号角,催促着一机集团必须尽快提升经济运行质量。党的十八大后,“发挥市场资源配置决定性作用”,军工领域深化改革的信号,更让一机人预感到:军品生产市场化竞争将更加严峻,把“全价值链体系化精益管理战略”升级为行业战略迫在眉睫。
“全价值链体系化精益管理”是中国兵器工业集团近年来提出的适应军工产品市场化竞争需要、全面提升全价值链各环节价值创造能力和企业基础管理水平的一项发展战略。其基本内涵为通过在全体员工中建立价值识别和以用户为中心的服务理念,将研发、采购、制造、营销等创造价值的主要环节,人力资源、财务金融、质量、安全、设备、能源、企业文化建设等创造价值的辅助环节,连接成一条全价值链,并围绕每个环节,灵活运用精益管理的思想理论、工作方法,对全部生产流程和管理进行系统性改善。与此同时,将整个组织推进过程上升为重塑企业文化的战略方针和决策,在所有管理领域、生产经营全过程大力推行,实现企业全价值链各环节价值创造能力和基础管理水平的显著提升。
作为兵器工业集团骨干企业的内蒙古一机集团在战略实施中提出:公司所有经营管理活动都要以精益思想和理念为统领;精益管理思想和工作要沿全价值链,全面覆盖公司各管理领域,贯穿经营管理全过程;以精确设计、精准生产、精品制造、精心管理、精打细算、精干高效为支撑,全面深入推进精益管理,用3—5年的时间使公司整体管理水平达到兵器第一、国内一流。
如今,践行精益管理3年多,一机集团正从内向外发生着精彩“蝶变”。
早在2011年6月,按照中国兵器工业集团统一部署,一机集团就已率先通过试点改革,探索精益化生产、精细化管理的新路。从精细到精益,从节约到增值,一机人不仅主动先行了第一步,而且,精益管理效果也开始逐年显现。
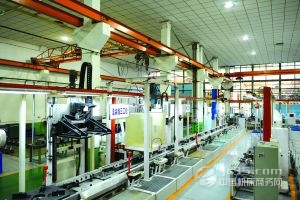
一机集团通过实施精益能源管理,使能耗大为降低。
一机集团四分公司的410车间:2011年生产成本支出292万元,2012年仅支出247万元;2011年的废品损失为9.2万元,2012年只有3.7万元;由于生产时间安排不合理,2011年给职工的加班误餐费就达4.2万元,2012年只有2.3万元。而特别值得一提的是支出的减少,是在任务量增加的前提下实现的。
一机集团宏远电器公司:按供应北奔重卡1万台电缆线束计算,2012年每台车节约电缆材料费19.79元,全年就节约资金近20万元。
“没想到多剪几公分,少剪几公分,差距竟然如此之大!”
一机人对“精益管理”的初始印象就在增收节支中明晰了,深化了。
此后的近3年间,通过精益生产思想理念的不断导入、精益示范区的持续建设,一机集团推进“全价值链体系化精益管理战略”的时机也渐趋成熟。
随着“精益管理”框架里的内容越来越丰富、越来越精细,精益研发、生产运营、精品制造及营销售后等环节的价值创造能力明显提升了!
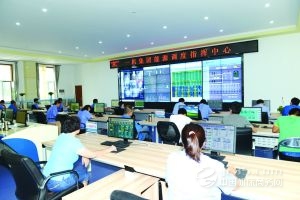
经过精益改造后的一机集团四分公司生产线。
走进一机集团的生产车间,无论新、老、旧厂房,全都干净、整洁,秩序井然。小到一个垃圾筒、一个零件,大到一台机床,都有其固定的位置,并做出图形、文字标识。
一机集团精益管理部门的工作人员介绍:“这是现场5S的体现,也是精益管理的重要基础之一。2011年,刚开始推行精益管理时,一机集团主要侧重于生产环节的改善,如今,这种改善除了在主价值链上不断深化,还外延至辅助价值链上。而精益管理也从开始时的‘一项活动’,被提升至战略层面—实现全价值链体系化精益管理。”
“全价值链体系化精益管理战略”提出:通过在全体员工中建立价值识别和以用户为中心的服务理念,将研发、采购、制造、营销等创造价值的主要环节,人力资源、财务金融、质量、安全、设备、能源、企业文化建设等创造价值的辅助环节,连接成一条全价值链,并围绕每个环节,灵活运用精益管理的思想理论、工作方法,开展系统性改善,同时,将整个组织推进过程上升为重塑企业文化的战略方针和决策,在所有管理领域、生产经营全过程大力推行,以实现企业全价值链各环节价值创造能力和基础管理水平的显著提升。
今年,一机集团制定出台了《精益管理5年规划纲要和发展路线图》,明确精益管理中长期发展目标,提出“三降、三提、两”—即降成本、降存货、降应收账款,提升产品实物质量、提升工作效率、提升现场管理水平,优化生产流程、优化管理流程系列工作目标,力争用3到5年时间,实现新产品研发周期、成本费用率、制造成本率、存货周转率、“两金”占用、全员劳动生产率等关键绩效指标同比改善20%以上。
同时,企业完善了以董事长为首的集团化管控系统组织领导体系;制定了精益管理考核办法,将54个二级单位统一纳入年度精益管理考核中,按照全面考核与重点突出相结合,分类制定标准,分区考核评价,分区域竞赛。
3年前,刚实施精益生产时,一机集团还是建框架,如今已开始不断向框架里充实内容。
如今,一机集团生产管理各环节的价值创造能力明显提升,在精益研发、生产运营、精品制造及营销售后等环节表现尤为突出。
在建立精益研发系统方面,科研部门以信息化手段为支撑,重点推进三维数字化精确设计,通过仿真模拟及分析,实现产品结构、关键零部件仿真优化及工件强度校核,逐步消除了设计过程中性能过剩、过度加工的浪费。通过协调设计平台的CAPP系统集成、设计及变更管理、借阅和打印管理、数据集中管理等,选择典型产品优化产品设计和管理流程,为科研试验能力提供保障。通过系统分析归纳产品研发水平的影响因素,从组织机构、体系细则、总体规划、V模式研发、数字化制造等多方面建设,探索出了更加适合军品精益研发管理的推进模式。工艺技术部门建立精益工艺体系,从数字化工艺编制、设计、品种规格标准化、材料定额等方面,开展精益工艺的编制工作,消除了工艺设计过程中浪费和不增值环节,促使工艺系统的核心业务流程得到有效优化并持续改进。
在生产运营系统中,重点解决了均衡生产、流程化生产过程的控制问题,推动了内部军品合同制实施,完善设备、能源、工装等专业化管理,实现了降存货、减少物流中间环节,消除了生产现场浪费与不增值环节。深化降本增效专项工程推动了经济运行质量持续改善,企业围绕13个领域的系统提升,梳理出16个方面、86个问题进行持续改进;从工艺改进与创新、原材料采购成本控制、节能降耗、人力资源挖潜增效、成本费用控制、“两金”占用控制等方面先后选择了25个降本项目持续改进,通过对“两金”占用、重点成本指标等的控制,使资产使用效率、运营效率、人员工作效率等方面得到提高,从而实现成本费用率每年在预算基础上再降0.5个百分点。
在建立精品制造系统方面,首先,对标兵器工业集团精益标杆单位及日本丰田汽车等国际先进企业,完善企业质量管理体系,打造军工企业特色的质量管理体系模式;其次,把质量管理培训当做最有价值的培训观念,注重企业技术人员、技能工人和质量管理者的技术业务培训,为质量管理创新能力储备实力;第三,狠抓质量管理制度的贯彻落实,通过积极引进新技术、新的管理方法,如“零缺陷”管理,卓越绩效模式、防错法、4M变化点管理等,实现产品质量的持续提升;第四,以质量管理部门牵头,生产、科研、工艺等部门具体实施,从“跑、冒、滴、漏、松、乱”精整开始、样车打造、标准固化、推广复制为重点,从强化防错技术等管理推广应用入手,探索从制造单元提升产品质量,对影响品质管控水平因素开展预期防控,力争每年实现质量损失率降低10%。
在营销售后系统中,积极推进生产型制造向服务型制造转变,从单纯卖产品、卖装备,向承包工程、设施维护和管理运营等一体化增值服务转变。出台实施一系列营销管理制度外,还建立了24家重点大客户档案。
此外,一机集团还建立起精益绩效激励机制,2014年,投入2000余万元,让广大员工分享改善的红利,以此为全价值链体系化精益管理提供动力源;实施了多个精益人才培训工程,为全价值链体系化精益管理提供能力源;实施了信息化和单元成本管控,为实现全价值链体系化精益管理提供保障;提升了各项基础管理水平,不断夯实“全价值链体系化精益管理战略”的基础;不间断地开展精益管理成果推广和宣传活动,塑造精益管理企业文化。
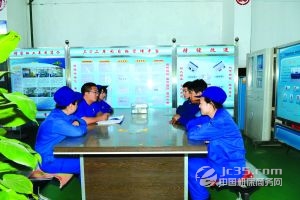
生产一线班组正在学习有关精益知识。
3年来,一机集团先后投资335万元,建立起包括公司精益研修中心、分子公司精益实践体验中心、车间班组精益学习园地三级人才育成基地,以大量模拟体验式培训,使精益管理培训更加贴近生产一线贴近实战,让受训者强化精益理念,掌握各种精益工具方法,达到“学练合一”的效果。一机集团有计划、分层次地培养各级各类精益人才共计21783人次,其中举办中、高层领导精益研修班12个,培养各领域精益管理领军人才110余名,举办精益班组长培训36期1440余人,实现了精益管理培训全覆盖。
精益求精的追求,使一机集团各项经营类指标大幅提升,那一连串的阿拉伯数字,就是一棵历经数十载风雨、自我更新的大树怒放出的春花!
今年,一机集团要求各单位将重点、要点、难点问题确定为改善项目,实施一批当年就能见效、见实效的亮点工程。从选择项目开始,各单位就慎之又慎。因为,一个项目若想通过,首先面对的是一层层的把关者对项目实施背景、资金来源、可行性、节创价值等因素的反复考量。一机集团现有40多人组成的精益专家库,每年不断更新,还外聘了咨询公司辅导。上半年,共有34个单位申报立项精益改善项目110项,内容涵盖军品和铁路车辆总装节拍化均衡生产能力建设、精益工厂设计、生产流程优化等,其中29个单位41个项目通过公司级立项。
目前,有些立项的效果已经显现。例如,精益研发系统实现某轮式产品设计周期缩短10%,新产品贡献率43.25%,勘误一次差错率降低10%,研发成本降低5%。而对于研制产品,工艺设计更改率逐年下降25个百分点,平均每年能减少因工艺设计变更造成的浪费达120万元以上。
生产运营系统实现了成本费用率每年下降1个百分点,初步打造出了国内第一条陆装总装4小时脉动式节拍化生产线。
营销售后系统实现了年均应收账款净额4655万元,同比下降15%。售后服务系统实现每年包装发运费用同比节约250万元以上。精品制造系统实现每年质量损失率同比改善1.2%以上,顾客满意度达到92%以上。
“全价值链体系化精益管理战略”的实施,使一机集团基础管理水平显著提升。近3年的合理化建议提案改善,累计创效19613.91万元,人年均节创价值3725元。
近3年的精益实践,使一机集团各项经营类指标均有大幅提升。2013年,一机集团实现主营业务收入105.1亿元,同比增长19%;实现利润4.5亿元,同比增长20%;全员劳动生产率14万元/人·年,同比增长11%。今年1到10月,公司累计签订销售合同140.7亿元,同比增长34.3%;实现主营业务收入87.1亿元,同比增长1.3%;实现利润3.2亿元,同比增长7.5%;实现全员劳动生产率12.9万元/人,同比增长10.7%。
如今,一机集团生产管理各环节的价值创造能力明显提升,在精益研发、生产运营、精品制造及营销售后等环节表现尤为突出。
在建立精益研发系统方面,科研部门以信息化手段为支撑,重点推进三维数字化精确设计,通过仿真模拟及分析,实现产品结构、关键零部件仿真优化及工件强度校核,逐步消除了设计过程中性能过剩、过度加工的浪费。通过协调设计平台的CAPP系统集成、设计及变更管理、借阅和打印管理、数据集中管理等,选择典型产品优化产品设计和管理流程,为科研试验能力提供保障。通过系统分析归纳产品研发水平的影响因素,从组织机构、体系细则、总体规划、V模式研发、数字化制造等多方面建设,探索出了更加适合军品精益研发管理的推进模式。工艺技术部门建立精益工艺体系,从数字化工艺编制、设计、品种规格标准化、材料定额等方面,开展精益工艺的编制工作,消除了工艺设计过程中浪费和不增值环节,促使工艺系统的核心业务流程得到有效优化并持续改进。
在生产运营系统中,重点解决了均衡生产、流程化生产过程的控制问题,推动了内部军品合同制实施,完善设备、能源、工装等专业化管理,实现了降存货、减少物流中间环节,消除了生产现场浪费与不增值环节。深化降本增效专项工程推动了经济运行质量持续改善,企业围绕13个领域的系统提升,梳理出16个方面、86个问题进行持续改进;从工艺改进与创新、原材料采购成本控制、节能降耗、人力资源挖潜增效、成本费用控制、“两金”占用控制等方面先后选择了25个降本项目持续改进,通过对“两金”占用、重点成本指标等的控制,使资产使用效率、运营效率、人员工作效率等方面得到提高,从而实现成本费用率每年在预算基础上再降0.5个百分点。
在建立精品制造系统方面,首先,对标兵器工业集团精益标杆单位及日本丰田汽车等国际先进企业,完善企业质量管理体系,打造军工企业特色的质量管理体系模式;其次,把质量管理培训当做最有价值的培训观念,注重企业技术人员、技能工人和质量管理者的技术业务培训,为质量管理创新能力储备实力;第三,狠抓质量管理制度的贯彻落实,通过积极引进新技术、新的管理方法,如“零缺陷”管理,卓越绩效模式、防错法、4M变化点管理等,实现产品质量的持续提升;第四,以质量管理部门牵头,生产、科研、工艺等部门具体实施,从“跑、冒、滴、漏、松、乱”精整开始、样车打造、标准固化、推广复制为重点,从强化防错技术等管理推广应用入手,探索从制造单元提升产品质量,对影响品质管控水平因素开展预期防控,力争每年实现质量损失率降低10%。
在营销售后系统中,积极推进生产型制造向服务型制造转变,从单纯卖产品、卖装备,向承包工程、设施维护和管理运营等一体化增值服务转变。出台实施一系列营销管理制度外,还建立了24家重点大客户档案。
此外,一机集团还建立起精益绩效激励机制,2014年,投入2000余万元,让广大员工分享改善的红利,以此为全价值链体系化精益管理提供动力源;实施了多个精益人才培训工程,为全价值链体系化精益管理提供能力源;实施了信息化和单元成本管控,为实现全价值链体系化精益管理提供保障;提升了各项基础管理水平,不断夯实“全价值链体系化精益管理战略”的基础;不间断地开展精益管理成果推广和宣传活动,塑造精益管理企业文化。
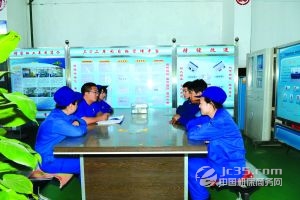
生产一线班组正在学习有关精益知识。
3年来,一机集团先后投资335万元,建立起包括公司精益研修中心、分子公司精益实践体验中心、车间班组精益学习园地三级人才育成基地,以大量模拟体验式培训,使精益管理培训更加贴近生产一线贴近实战,让受训者强化精益理念,掌握各种精益工具方法,达到“学练合一”的效果。一机集团有计划、分层次地培养各级各类精益人才共计21783人次,其中举办中、高层领导精益研修班12个,培养各领域精益管理领军人才110余名,举办精益班组长培训36期1440余人,实现了精益管理培训全覆盖。
精益求精的追求,使一机集团各项经营类指标大幅提升,那一连串的阿拉伯数字,就是一棵历经数十载风雨、自我更新的大树怒放出的春花!
今年,一机集团要求各单位将重点、要点、难点问题确定为改善项目,实施一批当年就能见效、见实效的亮点工程。从选择项目开始,各单位就慎之又慎。因为,一个项目若想通过,首先面对的是一层层的把关者对项目实施背景、资金来源、可行性、节创价值等因素的反复考量。一机集团现有40多人组成的精益专家库,每年不断更新,还外聘了咨询公司辅导。上半年,共有34个单位申报立项精益改善项目110项,内容涵盖军品和铁路车辆总装节拍化均衡生产能力建设、精益工厂设计、生产流程优化等,其中29个单位41个项目通过公司级立项。
目前,有些立项的效果已经显现。例如,精益研发系统实现某轮式产品设计周期缩短10%,新产品贡献率43.25%,勘误一次差错率降低10%,研发成本降低5%。而对于研制产品,工艺设计更改率逐年下降25个百分点,平均每年能减少因工艺设计变更造成的浪费达120万元以上。
生产运营系统实现了成本费用率每年下降1个百分点,初步打造出了国内第一条陆装总装4小时脉动式节拍化生产线。
营销售后系统实现了年均应收账款净额4655万元,同比下降15%。售后服务系统实现每年包装发运费用同比节约250万元以上。精品制造系统实现每年质量损失率同比改善1.2%以上,顾客满意度达到92%以上。
“全价值链体系化精益管理战略”的实施,使一机集团基础管理水平显著提升。近3年的合理化建议提案改善,累计创效19613.91万元,人年均节创价值3725元。
近3年的精益实践,使一机集团各项经营类指标均有大幅提升。2013年,一机集团实现主营业务收入105.1亿元,同比增长19%;实现利润4.5亿元,同比增长20%;全员劳动生产率14万元/人·年,同比增长11%。今年1到10月,公司累计签订销售合同140.7亿元,同比增长34.3%;实现主营业务收入87.1亿元,同比增长1.3%;实现利润3.2亿元,同比增长7.5%;实现全员劳动生产率12.9万元/人,同比增长10.7%。
如今,一机集团生产管理各环节的价值创造能力明显提升,在精益研发、生产运营、精品制造及营销售后等环节表现尤为突出。
在建立精益研发系统方面,科研部门以信息化手段为支撑,重点推进三维数字化精确设计,通过仿真模拟及分析,实现产品结构、关键零部件仿真优化及工件强度校核,逐步消除了设计过程中性能过剩、过度加工的浪费。通过协调设计平台的CAPP系统集成、设计及变更管理、借阅和打印管理、数据集中管理等,选择典型产品优化产品设计和管理流程,为科研试验能力提供保障。通过系统分析归纳产品研发水平的影响因素,从组织机构、体系细则、总体规划、V模式研发、数字化制造等多方面建设,探索出了更加适合军品精益研发管理的推进模式。工艺技术部门建立精益工艺体系,从数字化工艺编制、设计、品种规格标准化、材料定额等方面,开展精益工艺的编制工作,消除了工艺设计过程中浪费和不增值环节,促使工艺系统的核心业务流程得到有效优化并持续改进。
在生产运营系统中,重点解决了均衡生产、流程化生产过程的控制问题,推动了内部军品合同制实施,完善设备、能源、工装等专业化管理,实现了降存货、减少物流中间环节,消除了生产现场浪费与不增值环节。深化降本增效专项工程推动了经济运行质量持续改善,企业围绕13个领域的系统提升,梳理出16个方面、86个问题进行持续改进;从工艺改进与创新、原材料采购成本控制、节能降耗、人力资源挖潜增效、成本费用控制、“两金”占用控制等方面先后选择了25个降本项目持续改进,通过对“两金”占用、重点成本指标等的控制,使资产使用效率、运营效率、人员工作效率等方面得到提高,从而实现成本费用率每年在预算基础上再降0.5个百分点。
在建立精品制造系统方面,首先,对标兵器工业集团精益标杆单位及日本丰田汽车等国际先进企业,完善企业质量管理体系,打造军工企业特色的质量管理体系模式;其次,把质量管理培训当做最有价值的培训观念,注重企业技术人员、技能工人和质量管理者的技术业务培训,为质量管理创新能力储备实力;第三,狠抓质量管理制度的贯彻落实,通过积极引进新技术、新的管理方法,如“零缺陷”管理,卓越绩效模式、防错法、4M变化点管理等,实现产品质量的持续提升;第四,以质量管理部门牵头,生产、科研、工艺等部门具体实施,从“跑、冒、滴、漏、松、乱”精整开始、样车打造、标准固化、推广复制为重点,从强化防错技术等管理推广应用入手,探索从制造单元提升产品质量,对影响品质管控水平因素开展预期防控,力争每年实现质量损失率降低10%。
在营销售后系统中,积极推进生产型制造向服务型制造转变,从单纯卖产品、卖装备,向承包工程、设施维护和管理运营等一体化增值服务转变。出台实施一系列营销管理制度外,还建立了24家重点大客户档案。
此外,一机集团还建立起精益绩效激励机制,2014年,投入2000余万元,让广大员工分享改善的红利,以此为全价值链体系化精益管理提供动力源;实施了多个精益人才培训工程,为全价值链体系化精益管理提供能力源;实施了信息化和单元成本管控,为实现全价值链体系化精益管理提供保障;提升了各项基础管理水平,不断夯实“全价值链体系化精益管理战略”的基础;不间断地开展精益管理成果推广和宣传活动,塑造精益管理企业文化。
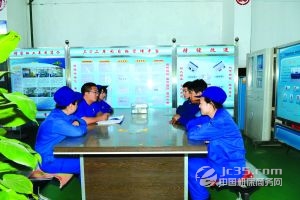
生产一线班组正在学习有关精益知识。
3年来,一机集团先后投资335万元,建立起包括公司精益研修中心、分子公司精益实践体验中心、车间班组精益学习园地三级人才育成基地,以大量模拟体验式培训,使精益管理培训更加贴近生产一线贴近实战,让受训者强化精益理念,掌握各种精益工具方法,达到“学练合一”的效果。一机集团有计划、分层次地培养各级各类精益人才共计21783人次,其中举办中、高层领导精益研修班12个,培养各领域精益管理领军人才110余名,举办精益班组长培训36期1440余人,实现了精益管理培训全覆盖。
精益求精的追求,使一机集团各项经营类指标大幅提升,那一连串的阿拉伯数字,就是一棵历经数十载风雨、自我更新的大树怒放出的春花!
今年,一机集团要求各单位将重点、要点、难点问题确定为改善项目,实施一批当年就能见效、见实效的亮点工程。从选择项目开始,各单位就慎之又慎。因为,一个项目若想通过,首先面对的是一层层的把关者对项目实施背景、资金来源、可行性、节创价值等因素的反复考量。一机集团现有40多人组成的精益专家库,每年不断更新,还外聘了咨询公司辅导。上半年,共有34个单位申报立项精益改善项目110项,内容涵盖军品和铁路车辆总装节拍化均衡生产能力建设、精益工厂设计、生产流程优化等,其中29个单位41个项目通过公司级立项。
目前,有些立项的效果已经显现。例如,精益研发系统实现某轮式产品设计周期缩短10%,新产品贡献率43.25%,勘误一次差错率降低10%,研发成本降低5%。而对于研制产品,工艺设计更改率逐年下降25个百分点,平均每年能减少因工艺设计变更造成的浪费达120万元以上。
生产运营系统实现了成本费用率每年下降1个百分点,初步打造出了国内第一条陆装总装4小时脉动式节拍化生产线。
营销售后系统实现了年均应收账款净额4655万元,同比下降15%。售后服务系统实现每年包装发运费用同比节约250万元以上。精品制造系统实现每年质量损失率同比改善1.2%以上,顾客满意度达到92%以上。
“全价值链体系化精益管理战略”的实施,使一机集团基础管理水平显著提升。近3年的合理化建议提案改善,累计创效19613.91万元,人年均节创价值3725元。
近3年的精益实践,使一机集团各项经营类指标均有大幅提升。2013年,一机集团实现主营业务收入105.1亿元,同比增长19%;实现利润4.5亿元,同比增长20%;全员劳动生产率14万元/人·年,同比增长11%。今年1到10月,公司累计签订销售合同140.7亿元,同比增长34.3%;实现主营业务收入87.1亿元,同比增长1.3%;实现利润3.2亿元,同比增长7.5%;实现全员劳动生产率12.9万元/人,同比增长10.7%。